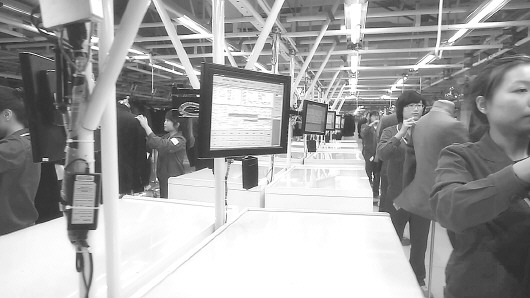
每个操作工位都有一台电子终端,可以显示订单的细节要求。资料片
红领集团究竟有什么过人之处,让正在向互联网思维转型的张瑞敏下命令,让海尔所有高管必须来红领学习?
海尔9次到红领集团取经,究竟取到什么经?
本报记者 张頔
11年前,张代理游历欧洲后,给红领选择了“定制”这条路;那时,中国人还不知道大数据这个概念。人们骂他神经病,“但现在你去别的服装厂看看,他们积压了多少存货,就知道不做定制才是神经病。”张代理说。
11年时间,几个亿资金。现在,当全中国的企业家都在吆喝互联网思维时,他们才发现,这个即墨裁缝早走在他们前面了。
量产“定制”:
在流水线上完成
红领集团的上装车间,各色款式不同的西服上装让人感觉这里并不像一个流水线车间,更像一家服装店的展示店铺。几百件上装颜色、面料不同,就连内里上的绣字、口袋的设置都是一件衣服一个样。
“从这些做好的西服就能看出来,我们的定制绝对是个性化的。”红领集团常务副总裁李金柱介绍,客户提供的订单包括了身材指标、细节设计等定制数据,在设计版型时用上了大数据技术。
对于定制服装来说,版型设计是关键一环,其意义相当于盖楼用的图纸。传统的正装定制由制版师傅量体后手工设计,一个熟练的版型师一天最多做两个版型,还会存在误差。现在红领每天能生产1200套定制西服,却不需要600位版型师,只需要在制版系统输入顾客身体数据和细节要求,一套个性化版型会自动生成。
整个定制生产流程包含着和制版系统类似的20多个子系统,全部以数据来驱动运营。版型定好之后,信息便会自动传输到布料部门,按照订单要求准备好布料后,裁剪部门马上按照要求进行裁剪。
裁剪后大小不一、颜色各异的布料佩戴上电子标签,便被送上车间上方的轨道开始在298道工序间自动流转。1500名工人每人面前有一个识别终端,扫描每块布料的电子标签,终端上显示出工艺标准和操作要求,工人就根据里衬、扣子、袖边等技术数据,进行手工或机械缝制。
这一过程虽然是流水线作业,但每件订单要求不同,比如一个缝制扣眼的工位上方,就挂着7排、每排15支不同颜色的缝线。
“比起传统手工定制,我们一道工序也没有省略,但通过数据系统和流水线结合,大大提高了生产效率。”李金柱说,国外西服定制一般都需要三到六个月,而在红领一套西服制作只需7个工作日,且都是一次制作完成,员工也从“在岗”工作转换为“在线”工作。
转型:
受宝马、奔驰启发
1995年,张代理创立红领集团,主打品牌成衣,2003年他打定主意做定制,几次海外考察促使了他这次转型。
在意大利,张代理见识了欧洲最正宗的服装定制。“那种手工工艺真是没得说。”张代理觉得,这样的高级定制西装动辄上万欧元,的确物有所值,但整套手工工艺却很难被复制。
在德国时,张代理特意拿出几天时间去宝马和奔驰公司参观。他发现流水线上生产出来的汽车居然不是一个样。经过喷漆环节后,有些车体是黑色的,有的是蓝色的。德国人说,这是按客户需要喷的,喷漆生产线可以根据订单随时替换不同颜色。
“汽车都可以在生产线上完成私人定制,那么定制服装为什么不可以通过优化工序来实现流水线上的量产呢?”这次参观给张代理的启发很大,他开始考虑用工业化手段来做定制服装,于是萌生了建立数据库的想法。
对于定制服装来说,身材数据的采集是首要的事,在行外人看来,量体并不难,拿着软尺贴身丈量不就行了?
事实上,传统定制服装工艺对量体师傅要求很高,他们采集的数据直接影响版型制作,合格的量体师傅需要长时间经验积累。
张代理聘请了一位有40多年经验的老师傅传帮带。然而两个月过去了,老师傅居然没教出一个合格的学生。师傅说,量体是件言传身教的活,没法速成。
张代理有些无奈,但量体方法必须准确简捷,否则就无法形成大规模工业化生产。这一门槛必须迈过。
张代理在纸上画了一个人形,开始“自主创新”——他先在人身上找了肩端点、肩颈点、颈肩端这几个参照坐标点,然后在中腰画了一条水平线,这就形成了三点一线“坐标量体法”的雏形。
目前“三点一线”量体法已经具有了自主知识产权,用一把尺子和一套量体工具(肩斜测量仪)便可进行点对点简单测量,采集人体19个部位的22个数据后,便可以对应设计出合身的版型。
标准化:
把复杂的事情做到最简单
“量体”只是定制服装的第一步,数据采集后关键是怎么用,通过什么样的模型将数据转化为版型。张代理成立了一个百人团队建模。
一位经历过数据系统筹建工作的技术人员介绍,计算规则制定好之后,更困难的还在后面——如何拆解成衣工序。因为定制的每件衣服都不一样,但又要实现流水线生产,而且整个拆解过程还得靠计算机系统自动形成,这是最核心也是最难的。“虽然现在成功了,但再让我去做我都不愿意,实在太难了。”
在这位技术员看来,把复杂的事情做到最简单,这就实现了高度标准化。这需要首先将成衣拆解到每道工序上具体应执行的工作;之后通过严密的算法程序,测算出大批量个性化生产每个点应该安排的工作量,每道工序的工作时间等,在样衣车间测试完后到生产线上去做,避免产能浪费。
红领最初把定制服装和流水线结合时,还没有如今的信息化设备。但张代理推行流水线定制的决心很强,他直接把每件订单的各个工序写在纸上,每个工人操作前先在纸上找数据。由于纸张容易断裂,后来换了长条布幅,一两百道工序都编成代码写在上面。
李金柱当时在车间负责生产,那种“刀耕火种”的场景还历历在目。因为是手写,有些工序代号字母和数字容易混淆,比如字母q和数字9,字母b和数字6有时就分不清。这也导致一个工序出现问题,整件定制西服可能就要返工。
研发过程中折磨人的地方还在于量体、版型、工艺、裁剪和流水线问题需要同步解决。有时后边工艺问题解决了,前面大数据系统的建模规则却进行了改动,于是一切只得推倒重来。“很多人为什么烦?加班加点做了半年时间,做到最后结果还得全部废掉重来。”李金柱当时也免不了要抱怨几句。
最初红领拿出一个班组测试,然后扩展到一条流水线,再扩展到一个车间、两个车间、三个车间,最终用了11年时间和数亿经费,才达到了目前这样的效果。
“最早很多人都和我对着干,不和我对着干的人很少。”张代理说,刚研发数据系统时,正好是西服市场井喷的时候,批量成衣都卖到供不应求,厂里不少人不理解他为什么要坚持定制这条路。
“当时甚至有人说我是神经病,但现在你去别的服装厂看看,他们积压了多少存货,就知道不做定制才是神经病。”张代理说,目前红领60%的产能都是定制服装,订单大多来自海外,其中美国占60%、欧洲占30%,国内占10%,光是纽约市场每天定制产品就达400套。
本稿件所含文字、图片和音视频资料,版权均属齐鲁晚报所有,任何媒体、网站或个人未经授权不得转载,违者将依法追究责任。