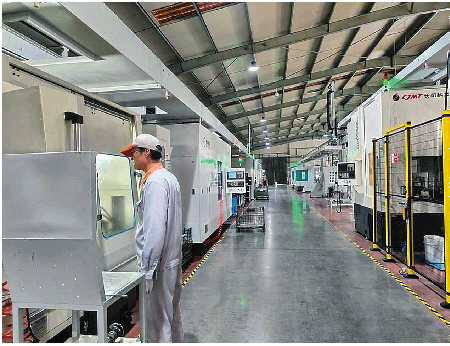
青岛德盛偌大的生产车间内,只有很少的技术工人负责生产线运行监控。
新世纪前夕,这家青岛的制造企业发不出工资、付不起货款,随时可能倒闭。如今,它已经成为一家高端发动机曲轴的研发制造企业,是德国宝马、意大利比亚乔、日本本田等知名摩托车品牌的首选供应商。从倒闭边缘到隐形冠军,智能化升级起了关键作用。它也是众多青岛制造企业的缩影,不断向新求变,用智能化给企业带来新的发展。
文/片 宋祖锋 青岛报道
智造转型标杆曾濒临倒闭
3月13日,在位于青岛平度市的青岛德盛智能化生产车间里,机器轰鸣,一台台关节机器人正在从物料架上抓取锻造好的曲轴毛坯,灵活自如的机械臂将毛坯稳稳送入数控机床加工工位。经过一道道智能化生产程序,一支支精密的曲轴从生产线上诞生。记者注意到,偌大的生产车间内,只有几名技术工人负责生产线运行监控。从2013年首条发动机曲轴智能化生产线投产运行,到如今建成8条高端大排量曲轴智能化生产线,青岛德盛缔造了行业内从制造到智造的转型标杆。
然而,大众或许很难想到,这家标杆企业曾经也一度濒临倒闭。
成立于1957年的青岛德盛,原本是一家以生产农具为主的国有企业。随着经济社会发展,企业也从传统的农具制造逐渐向摩托车发动机曲轴生产转型。1999年,彼时的青岛德盛主要生产小排量摩托车发动机曲轴。“那段时间,公司账上没钱,发不出工资,付不起货款,企业随时可能倒闭。”青岛德盛党委书记、总经理罗赛说,产品技术含量低、附加值低,市场竞争力弱,各种因素叠加致使企业经营难以为继。
面对困境,德盛人没有放弃,只要有一线生机,他们就愿意付出百倍努力。为了寻找新的订单,新上任的企业党委书记、厂长孙佩璋决定亲自带队出差,拜访客户,开拓市场。然而,公司财务账上已经拿不出差旅费。为了凑齐差旅费,公司低价卖掉别的客户折抵货款的摩托车,凑齐了3000元差旅费。
功夫不负有心人。在孙佩璋的带领下,公司全体员工齐心协力,订单逐渐增多,企业走出困境迎来新生。“那段困难时期的经历,是我们公司最宝贵的财富,也塑造了我们百折不挠、坚强不屈的企业精神。”罗赛说。
2005年企业改制成为民企后,企业开始引入现代管理制度,优化生产流程,并加大技术研发投入。通过引进先进的生产设备和技术,青岛德盛逐步提升了产品的技术含量和附加值,增强了市场竞争力。同时,企业还积极拓展国内外市场,与三十多家世界知名企业建立了战略合作关系。
智能化转型开启新篇章
当大多数企业对“智能化”概念还停留在理论阶段,青岛德盛已经开始将智能化理念付诸实践。2011年,青岛德盛敏锐地意识到智能化是企业发展的必由之路,当时国内外没有曲轴智能化生产线的资料或经验可以借鉴,一切要靠自己摸石头过河。谈及企业智能化转型开端,用公司数字化研发中心主任崔京章的话说,“处处是难题”。
时光回溯到2011年5月,青岛德盛购置第一台日本川崎关节机器人运用到生产线,进行单元式智能化生产试验,获得了智能化生产组建经验。然而,智能化转型之路并非坦途。没有经验,他们就到处参观学习;没有技术,他们就四处登门求教。经过两年的实验、筹备,攻关克难,2013年,青岛德盛第一条智能化生产线终于投产。
然而,期待已久的喜悦却被一盆冷水浇灭。“投产第一个月,那时候机器运行总是不稳定,生产出来的曲轴尺寸精度不达标,废品率居高不下。” 3月13日,在青岛德盛第一条智能化生产线前,看着眼前一台台仍在运行自如的关节机器人,崔京章颇有感触。面对当时突如其来的问题,研发人员满是焦虑和迷茫,但大家只能迎难而上。
大家夜以继日地工作,对生产线上的每一个环节进行仔细排查,不放过任何一个细节。“我们排查了几百个可能影响产品质量的因素,最终找到了问题的根源。”崔京章说,原来,问题出在生产线控制系统的线路面板上,由于一个焊头没有焊牢靠,导致设备运行不稳定,最终影响了产品质量。找到问题根源后,智能化生产线终于实现了稳定运行。该智能线的建成投产,也创造了中国摩托车曲轴智能化生产的先河,为行业数智化发展形成了可复制的技术。
有了智能化生产线的加持,青岛德盛生产效率比之前传统人工生产提高两三倍,曲轴精度达到千分之一毫米级别,相当于头发丝直径的十分之一。
这只是青岛德盛从“制造”向“智造”转型迭代之路上的一个缩影。有了第一条智能化生产线建设经验,青岛德盛陆续建成德国宝马发动机曲轴智能化生产线等多条高端大排量整体多缸曲轴智能化生产线,曲柄销智能化生产线,德国宝马发动机曲轴智能化生产线和热处理智能化生产线,实现离散式工业高精密曲轴的智能化生产,为在行业中率先实现中国制造2025和工业4.0奠定了基础。
高水准智造带来全球客户
从小排量发动机曲轴到大排量发动机曲轴,再到高端发动机曲轴,青岛德盛在追求卓越的道路上永不停歇。
曲轴并非标准件,每款发动机的也都不一样。“主机厂客户提供图纸,怎么生产都是我们自己摸索实践。”罗赛说,有一次,青岛德盛机械接到了一批具有国际最高水平的高端发动机曲轴的订单。与以往不同的是,这次客户对曲轴的精度、强度和耐磨性提出了更高的要求,并且提供了全新的设计图纸,这对德盛来说是机遇也是挑战。
罗赛说,一个曲轴需要上百道工序,仅仅制作一个样品就需要45天。由于客户要求的新产品与公司现有生产工艺存在较大差异,研发团队在试制过程中遇到了诸多困难。“刚开始试制出来的曲轴,总是存在各种问题,要么精度不达标,要么强度不够,要么耐磨性差。”回忆起研发过程,罗赛感慨万千。新产品工艺流程烦琐复杂,研发团队最初试制出来的样品,总有一道程序不合格,达不到图纸要求。为了攻克技术难关,罗赛带领研发团队日夜奋战,反复论证试验,不断调整工艺参数,优化加工流程。
那段时间,罗赛和同事们经常工作到深夜,研发中心里灯火通明,遇到技术难题,大家反复论证试验。经过几十次试验,研发团队终于找到了最佳工艺方案,成功研制出符合客户要求的曲轴样品。最终,青岛德盛在规定时间内将高端曲轴样品交付客户,并获得了客户的高度评价。
近年来,随着全球制造业的转型升级,高端发动机曲轴市场需求持续增长。作为国际最高水准的德国宝马、美国哈雷、日本本田、意大利比亚乔等国内外80多家著名企业及国家重点产品的首选供应商,青岛德盛产品远销30多个国家和地区,新产品的不断研发厥功至伟。
3月13日,在青岛德盛科技文化馆内,陈列着几十款不同型号的高端曲轴,从高端摩托车、沙滩车,到船用舷外机和无人机,每一件高端发动机曲轴都闪耀着科技之光。目前,青岛德盛生产的高端产品包含单缸、双缸、三缸、四缸、六缸全系列曲轴产品,其中行业最有前景的四缸摩托车曲轴研发成功并已量产。“我们目前研发生产的曲轴品种达到上千个,年生产高端大排量多缸曲轴300多万套。”罗赛介绍,他们研发制造的四缸摩托车发动机曲轴约占90%的国内市场份额。
从一家经营困难的企业到如今高端发动机曲轴生产行业标杆,青岛德盛的转型之路,正是中国制造业从“制造”迈向“智造”的缩影。罗赛说,未来,青岛德盛将继续以创新为驱动,以智能化为引领,推动高端曲轴技术实现新突破。